One of the most important ways we can add value to an injection molded part is by fine-tuning its design to optimize manufacturability. This capability paid off recently on a molded assembly for a mask and trigger we produce for Oxygen Plus (O+), a company that has developed a successful recreational oxygen product.
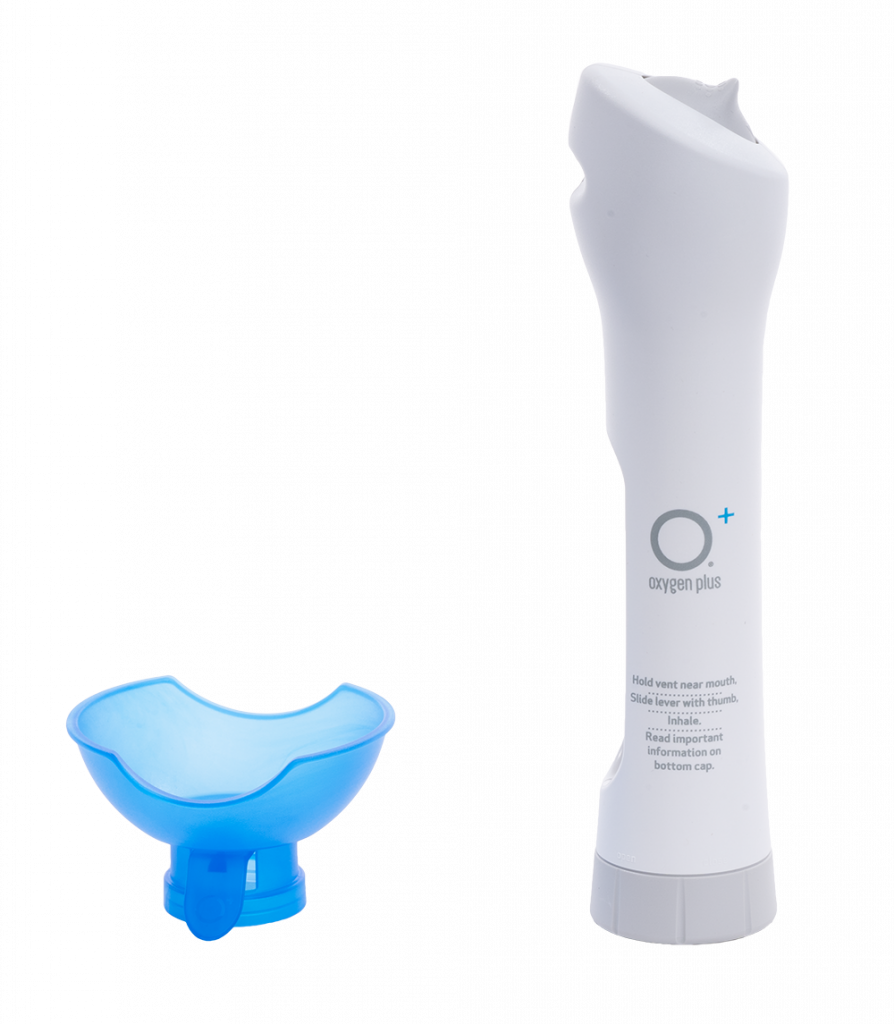
Called the O+ Biggi, the finished product includes a handheld oxygen canister with an integrated polypropylene mask and trigger assembly, the latter of which we produce. While the O+ Biggi isn’t a medical product, the mask assembly still needed to meet stringent cleanliness standards, as our customer assembles and fills its oxygen products in a FDA-registered facility. Our “white wall” molding facility, which includes clean all-electric molding machines, was a natural fit for the job.
Going further than churning out parts to an existing spec, we also worked with Oxygen Plus to optimize the mask and trigger design for manufacturability (DFM). The DFM efforts focused on two main goals:
- Reduce complexity to help Oxygen Plus reach its per-part cost targets.
- Support seamless scalability to make sure our production could scale seamlessly with our customer’s success.
We started with the complexity reduction, helping redesign the mask and trigger as a two-piece assembly with molded-in features on both parts to enable a quick snap-fit assembly process. Initial designs of the mask and trigger assembly consisted of four parts and an ultrasonic welding operation, so the new design was a success from a cost-reduction standpoint.
The redesign also resulted in a more functional part with wall thickness transitions from roughly 0.030 to 0.090 inches. The wall thickness transitions, which we are able to mold consistently without leaving blemishes and sink marks, make the mask pliable around the face while adding strength near the canister interface.
The reduction in parts count also contributed to the scalability goal. It is much easier to produce a simple two-piece snap-fit assembly at high volumes than an assembly that requires a secondary ultrasonic welding step. We also addressed scalability up front through our tooling design and sourcing capabilities.
Our ability to scale this job seamlessly turned out to be essential. The Oxygen Plus product we helped create has become a huge success in the consumer market, with production volumes jumping by an order of magnitude in a matter of months. Our molding operation was able to keep pace thanks to our forward-thinking partnership, the simplicity of the new design and our tooling strategy.
Do you have a part or assembly you’d like us to look at? Get in touch, and we can review your project together.